Sintered Bronze Filter Disc
Product Characteristics
Manufacturer | DALON |
Material | POROUS BRONZE |
Product Code | SBF |
Pore Pitch: | from 5 µm to 150 µm |
Diameter: | from 2 to 250 mm,and length from 2 to 1500 mm |
Porosity: | 35 up to 45% |
Density: | from 4.5 to 5.5 |
Traction: | resistance 3-6kg/mm2 |
Dilatation: | coefficient 17x10-6 |
Working Temp: | 200°C -MAX |
Specifications
Standard Geometries
Outside Diameter ØD | Ø 4mm to Ø 300mm |
Thickness | up to h 100mm |
Material | CuSn8 / CuSn10 |
Area Result:
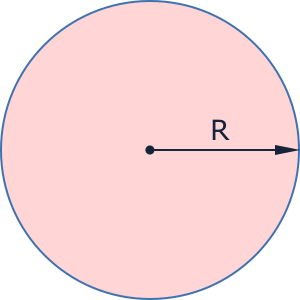
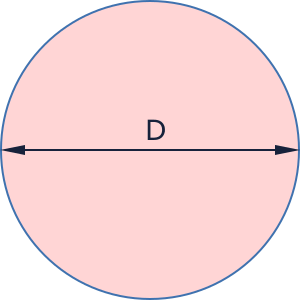
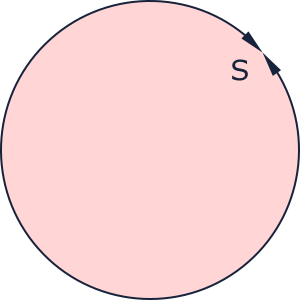
Sintered Bronze Filter Disc
An Essential Component for Advanced Filtration Solutions
- In the world of industrial filtration, the sintered bronze filter disc stands out as a paragon of efficiency and reliability. DALON as a leading supplier of these sophisticated components, we take pride in offering a product that is not only top-notch in quality but also versatile in its application across various industries.
- The Making of a Sintered Bronze Filter Disc:
- - Crafted through a process known as sintering, these filters are made from bronze powder. This method involves heating the powder below its melting point, causing the particles to bond without liquefying. The result is a highly porous yet structurally robust disc. This unique composition allows for excellent permeability while maintaining impressive strength and resistance to wear.
- Key Features and Benefits:
- - High Filtration Efficiency: The interconnected pore structure of the sintered bronze filter disc ensures superior filtration capabilities. It effectively removes contaminants from gases and liquids, providing a high degree of purity.
- - Thermal and Chemical Resistance: Bronze, being an alloy of copper and tin, naturally exhibits excellent resistance to corrosion and can withstand high temperatures. This makes these filters ideal for harsh chemical environments and high-temperature applications.
- - Long Service Life: Due to their robust construction, these filters offer an extended service life compared to traditional filters. This durability translates to fewer replacements, reduced downtime, and overall cost savings.
- - Customizable Pore Sizes: We understand that different applications require different filtration grades. Hence, our sintered bronze filter discs come in a variety of pore sizes, ensuring that you get the exact level of filtration needed for your specific process.
- - Easy to Clean and Maintain: The structure of these filters allows for easy cleaning, often simply by backflushing with a fluid, thus ensuring consistent performance and a longer operational lifespan.
- Commitment to Quality and Sustainability:
- DALON sintered bronze filter discs are not just about performance; they are also a testament to our commitment to quality and sustainability. We ensure that all materials used are of the highest grade, and our manufacturing processes are designed to minimize environmental impact.
- Understanding that every filtration challenge is unique, we offer customized solutions to meet your specific requirements. Our team of experts is always available to provide support and advice, ensuring that you get the most out of our products.
- Our sintered bronze filter discs represent the pinnacle of filtration technology. With their unparalleled efficiency, durability, and versatility, they are an invaluable tool for any industry looking to enhance their filtration systems. As your trusted supplier, we are here to provide you with a product that not only meets but exceeds your expectations.
Application Examples:
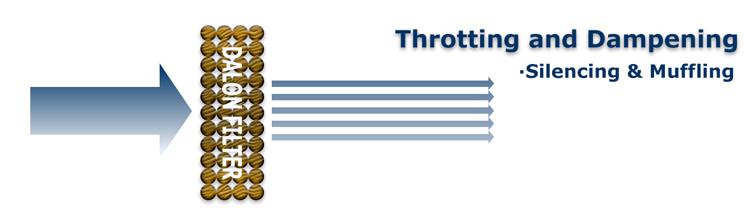
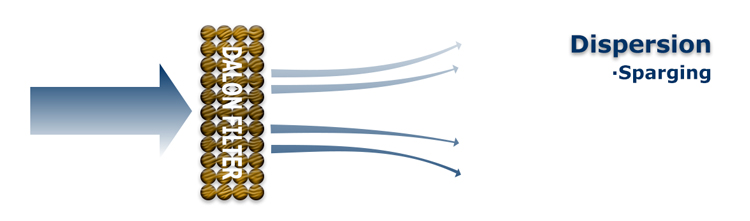
CHEMICAL INDUSTRIES | SEMICONDUCTOR |
SCIENTIFIC INSTRUMENT | PHARMACEUTICAL |
POLYMER FILTRATION | GAS AND LIQUID FILTRATION |
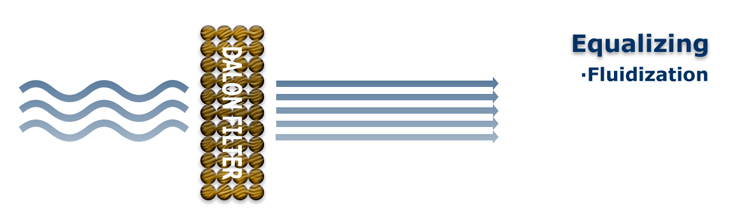
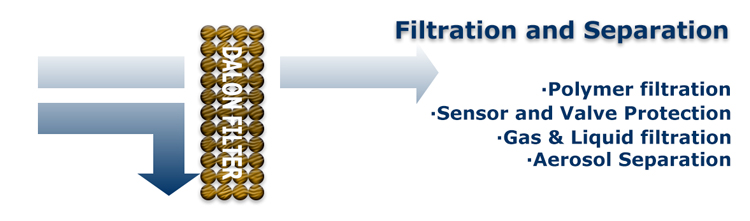
SILENCING | SPARGING |
FLUIDIZATION | SENSOR AND VALVE PROTECTION |
FLOW RESTRICTION | HANDLING OF BULK MATERIAL |
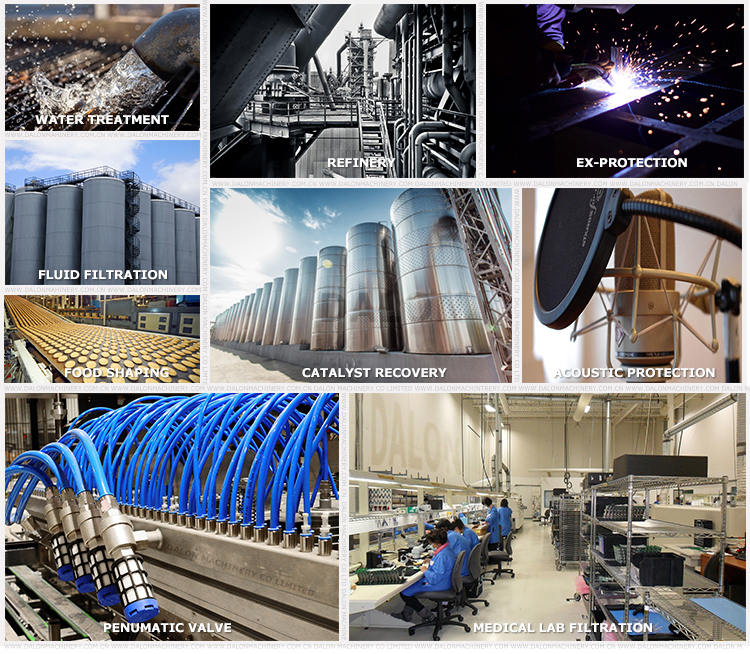
- Applications Across Industries
- The versatility of sintered bronze filter discs makes them suitable for a wide range of applications. Key industries that benefit from these filters include:
- Petrochemicals:
- - For filtering impurities in fuels and lubricants.
- Pharmaceuticals:
- - In the production of medicines, where purity is paramount.
- Food and Beverage:
- - Ensuring the safety and quality of products.
- Aerospace:
- - For filtration in complex and high-demand systems.
- Hydraulics:
- - In hydraulic systems where clean oil is crucial for performance.