What is the production process of powder metallurgy
Technical Article
Introduction
- Powder Making
- Mixing Powder
- Forming
- Sintering
- Post-treatment
Production Procedure
1. Milling: Milling is the process of turning raw materials into powder. Commonly used milling methods include oxide reduction method, atomization method, electrolysis method, rotating electrode method, and mechanical crushing method.
2. Mixture: Mixing is the process of mixing various required powders in a certain proportion and homogenizing them to make powder blanks. The mixing method is divided into three types: dry type, semi-dry type and wet type. During the powder pre-mixing process, due to the different specific gravity of the particles of different components, segregation will occur during the powder mixing process. The binder effectively improves segregation. Due to the different particle sizes in the powder, uneven distribution can easily lead to an increase in porosity. The binder It can make the particles distribute reasonably, fill the pores, and improve the strength of the green part.
3. Forming: Forming is the process of putting the uniformly mixed mixture into a die and pressing it into a parison with a certain shape, size and density. Commonly used methods for forming include room temperature press forming and heating press forming. Lubricant can effectively reduce internal and external friction, reduce the loss of pressing pressure, increase the density of the compact, reduce the demoulding force during the demoulding process, extend the service life of the mold, and ensure that the parts have a better surface finish.
4. Sintering: Sintering is a process that causes diffusion, welding, recrystallization and other processes between particles through melting, so that the powder particles are firmly welded together, reducing the pores and increasing the density, and finally obtains a "crystal combination", thus obtaining the desired A process that requires certain physical and mechanical properties.
5. Post-processing: Powder metallurgy products can be used directly after sintering; but when the performance requirements of the product are high, post-processing is often required. Commonly used post-processing methods are as follows:
Shaping: Put the sintered parts into a shaping mold with a similar structure to the compression mold, and press it again on the press to improve the dimensional accuracy of the parts and reduce the surface roughness of the parts, which is used to eliminate the problems in the sintering process. The slight deformation caused by it.
Oil impregnation: the process of putting the parts into hot oil at 100~200 °C or making the oil penetrate into the pores of the powder parts under vacuum. Parts soaked in oil can improve wear resistance and prevent parts from rusting.
Steam treatment: Iron-based parts are treated in water vapor at 500~600℃ to form a hard and dense oxide film on the inner and outer surfaces of the parts, thereby improving the wear resistance of the parts and preventing the parts from rusting.
Vulcanization treatment: Place the parts in a molten sulfur tank at 120°C, take them out after ten minutes, and reheat to 720°C under hydrogen protection to form sulfide in the pores on the surface of the parts. Vulcanization treatment can greatly improve the friction reduction and processing performance of parts.
Sintered Iron Bushing
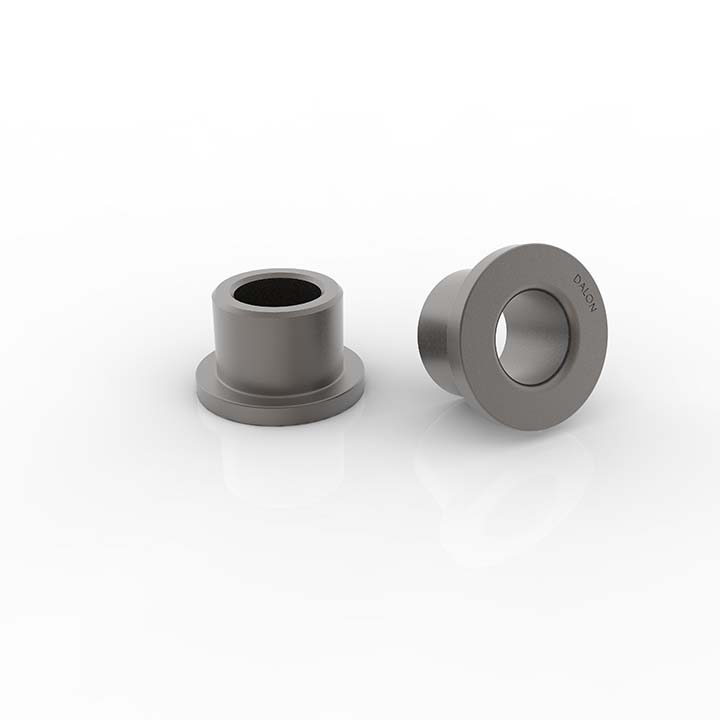